A new platform for fruit picking
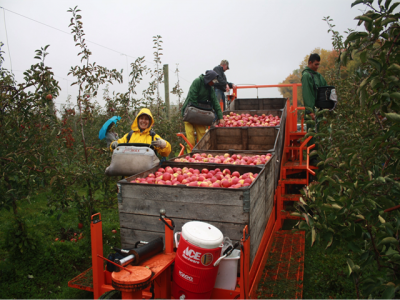
The use of picking platforms for fruit tree management and harvesting is still relatively new in South Africa. Thomas Babl, who has been using the technology for the past two years, shares some of the lessons he has learnt with Glenneis Kriel.
When Thomas Babl saw a picking platform for the first time at a field day at Paardekloof in the Witzenberg valley, he was sold on the idea. “The concept made so much sense,” he recalls. “Instead of workers having to carry ladders and climb up and down them in an orchard, they could stand on a moving platform to reach those difficult places. It’s not only easier for the workers, but enhances work speed.”
Thomas, who began using the technology two years ago, farms stone fruit at Lindenhof, between Simondium and Paarl in the Western Cape. He produces plums, peaches and nectarines on 20ha, which he wants to expand to 30ha. He estimates that, since utilising picking platforms, picking is about 30% faster, and thinning of flowers is up to 40% faster.
“It’s difficult to quantify savings, however, as there are so many variables to take into account. Workers took almost a year to get used to the platforms and realise that it was there to help them, not force them to work faster,” he says.
The use of platforms has not replaced workers; instead, it has allowed him to employ workers more efficiently. He can now employ older, less physically capable people who would have struggled to carry ladders around. “It has also made us less dependent on seasonal workers and enabled us to expand production without having to employ new staff,” he says.
Cutting costs
As labour is still cheaper in South Africa than in, say, Europe and Australia, few South African farmers are using the technology, explains Thomas. This has resulted in a limited choice of brands and machines. Thomas researched availability elsewhere and found a company in Italy that sold reconditioned platforms. He registered as an importer and bought two second-hand BerMarTec Knecht platforms at about R270 000 each – about half the price of a new one.
He was so impressed with the machines that he bought two more at the start of the year. Unfortunately, these platforms were more expensive, owing to the depreciation of the rand against the euro. According to Thomas, there was little risk in buying the platforms second-hand, as they had been overhauled by the factory and were as good as new. In addition, the platforms move slowly, and are thus subjected to very little wear and tear. “If you look after it, a platform can easily last 15 to 20 years, in comparison with tractors, which usually last only 10 years,” he says.
Energy efficiency
Thomas’s choice of model was based on energy efficiency. “With diesel becoming so expensive, it made more sense to buy an electric platform. Batteries of the electric platform last for a day or two, depending on how fast you’re driving, and cost only R5 to recharge,” he explains. In addition, an electric system’s running costs are lower than that of a diesel one, as the former requires no servicing. A battery operates for approximately 5 000 hours before needing replacement.
It is for the same reason that Thomas did not buy or build a platform pulled by a tractor. “With this method, you’ll not only have high diesel costs, but have to employ a tractor driver,” he explains. A downside is that the battery-operated machines are smaller and slower than their diesel counterparts. Thomas’s platforms drive at a maximum speed of 3km/h, while a diesel platform can reach up to 15km/h. His battery-operated platforms must therefore be towed to the orchards.
“At first we towed the platforms separately, but later we learnt that we could link them and tow them all at once,” he explains. The platforms are transported to the orchards before the start of work in the morning, or during lunch, to ensure they are ready for the workers.
Training
The Knecht can expand to a maximum width of 3,4m, making it too narrow for some of the older orchards, with row widths of 4m. The platforms must thus go down every row, instead of every second row, as would be the case with a larger platform or smaller row spacing. Thomas has found a fruiting wall canopy to be the ideal training system. New orchards are on a Palmette training system, where trees are planted 1,5m apart, with a row spacing of 3m to 3,5m. Trees are kept at a maximum height of 3,4m.
He stresses that excellent supervision is required with higher trees, as the pickers tend to neglect the mid-zone of this case. The platform uses an ultrasound sensor to steer automatically. This can be problematic at times as movement might be impeded by high weeds, or the absence of a tree in a row.
The platforms do not operate efficiently in old orchards, with many branches hanging into the rows. For this reason, Thomas uses the platforms in these orchards only to prune trees; once the fruit starts to ripen, picking and management practices are carried out on ladders. “The risk of fruit damage is simply too high,” he says.
Changing practices
With platforms, Thomas’s workers no longer use the traditional bin-on-a trailer collection method. This entails picking fruit and loading it into bins carried on a trailer pulled slowly between the rows. Once the bins are full, they are transported to the packhouse and the tractor returned with empty bins.
Thomas’s new method involved the use of custom- made machinery built to designs he saw on the Internet, as none was available in South Africa. In the new system, the bin is attached to the front of the platform. Once full, it is left in the row and collected later by a self-loading bin-trailer and a tractor.
“The new system is not only more fuel efficient, it has potential to greatly save time, once the workers get used to it,” Thomas says. He has found that it is best to limit the number of workers on the platform to two. Using more labourers on the platform is awkward due to the limited space. Labourers who are not on the platforms pick fruit from the lower parts of trees, on foot.
Thomas has also found that it is easier and more efficient for the four platforms to start and move forward together down the row, rather than drive ahead of each other.
Có thể bạn quan tâm
Phần mềm

Phối trộn thức ăn chăn nuôi

Pha dung dịch thủy canh

Định mức cho tôm ăn

Phối trộn phân bón NPK

Xác định tỷ lệ tôm sống

Chuyển đổi đơn vị phân bón

Xác định công suất sục khí

Chuyển đổi đơn vị tôm

Tính diện tích nhà kính

Tính thể tích ao hồ