An inside look at Sino Agro Foods giant prawn MegaFarm
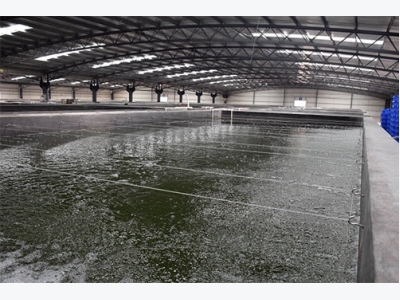
APRAS model in Zhongshan, China, a ‘paradigm shift’ in 21st century aquaculture
First set of tanks being filled at the MegaFarm for test trials.
Sino-Agro Foods, Inc. (SIAF) is a U.S.-incorporated, vertically integrated, protein-food company, with primary operations in the People’s Republic of China (PRC). Its business sectors include beef cattle, organic fertilizer, feeds, aquaculture and seafood sales and consulting. The company, which is currently publicly traded on the OTCQX in the United States, and Merkur Market of Oslo Bars in Norway, posted $429 million in revenues in 2015.
Ongoing operations at Prawn Farm 1. production capacity of 1,000 metric tons per year. All photos courtesy of Sino Agro Foods.
SIAF operates several aquaculture farms and systems, indoor and outdoor recirculating aquaculture systems (RAS) that produced 6,762 metric tons (MT) of aquatic products in 2015. It is currently building what will be the world’s largest, indoor RAS farm, targeting a minimum production of 100,000 MT per year of giant freshwater prawns (Macrobrachium rosenbergii), Asian cod (Oxyeleotris marmoratus), and freshwater eels (Anguilla marmorata). The farm is designed from a biological perspective to achieve a maximum annual production of 300,000 MT.
Paradigm shift
Global aquaculture production is dominated by inland, pond culture (FAO, 2014), with RAS aquaculture contributing less than 0.04 percent of all grow-out production (excluding salmon smolt production). Although RAS production has many environmental and socio-economic advantages, high capital costs have hampered its economic feasibility to a large extent. In salmon, for instance, RAS culture only yields a return on investment (ROI) of 4 percent, compared to net pen culture of 53 percent (Boulet et al., 2010). The general consensus is that RAS is not profitable unless production of 10,000 MT or more is achieved, and that more research and development is needed to reduce costs or increase per-unit production, although notable exceptions exist.
Production of giant freshwater prawns using the APRAS technology: A. One-gram prawn juveniles; B. Adult prawns; C. Prawns utilizing substrate in APRAS tanks - substrate increases surface area and space utilization in the production tanks; D. Stage 2 growout of prawns using substrates to increase surface area and density.
For the past 11 years, SIAF has refined its proprietary A-Power Recirculating Aquaculture System (APRAS), production strategy, and target markets in China to overcome the barrier of high capital costs. While this technology is proprietary and simplified to reduce capital expenditure (CapEx) costs initially, it is the overall production strategy of high product turnover rate and niche target markets that yield such high production volumes and profitability. This strategy is a paradigm shift in thinking about how to achieve profitable and sustainable aquaculture.
The production of our system is based on a phased grow-out and partial harvest strategy (Fig. 1) that targets maximum yield (MT/mu/year.; one Chinese mu = 1/6 acre = 1/15 hectare). Because of faster product cycles and higher turnover coupled with year-round and stable indoor farming environmental conditions, the projected production (MT/year) is more than 13 times and the projected yield is more than 100 times higher than those of traditional pond culture of penaeid shrimps. Its income (revenues minus costs) generation is more than $5,000/square meter/year, compared to what can be calculated for salmon net pen culture at $500/square meter/year (Boulet et al., 2010), and tilapia RAS culture (Watanabe et al., 2002) at $200/square meter/year. As a result, the initial CapEx ROI of our system is more than three times higher than profitable net pen salmon culture.
Figure 1. Schematic of the SIAF APRAS production strategy (example in 1.5 space of a 3 building production unit) compared to traditional shrimp pond culture systems in China. A phased growout, and partial harvest strategy yields annual production (MT/yr.) 13 times higher and yield (MT/mu/yr.) over 100 times higher than traditional pond culture of penaeid shrimps. Animals are overstocked initially in stage 1 tanks, raised to a maximum density, then that batch is progressively moved and partially harvested throughout its growth cycle into separate tanks until final stage 4 growout, after which the remaining animals in the batch are all harvested. Emptied tanks are restocked approximately every 3-4 weeks, with successive batches yielding an average of 14 cycles/year in our system, compared to only 2 cycles/year in the “all in, all out” production strategy of many traditional pond culture systems.
Chosen species for our system are based on adaptability to its strategy and market price. New species are currently being tested and their production fine-tuned to adapt to changing market conditions in China.
Market
Food is central to the Chinese culture, and consumers with higher income levels are willing to pay comparatively higher prices for more, higher-valued seafood (Fig. 3). Per capita consumption of seafood in China is 31.5 kilograms per year, more than double the world average of 15 kg. (FAO, 2014). Live seafood products are more highly prized and traditional among Chinese, and higher-valued species are being increasingly demanded by a growing middle class.
We estimate that, because of the rapidly rising middle class in China (Song & Chu, 2009), an additional 6 million MT of high-value seafood will be required by 2025 to supply increasing demand. The World Food Bank (2013) estimates a total 13 million MT more seafood will be needed in China by 2025. We believe there will be a shift in seafood consumption towards more high-value and live product. Moreover, there is increasing demand by the middle class for improved food quality, safety and environmentally and socially sustainable farming practices in the country.
Fig. 2. Recent (2016) retail prices for seafood at a mid-range seafood restaurant in Zhongshan, China. Prices range from $19-23/kg. for giant freshwater prawns and Pacific white shrimp, to upwards of $73/kg. for Alaska king crab and $113/kg. for various groupers. Chinese consumers purchase the entire animal, so a single dish of grouper can cost up to $565, as one of eight dishes traditionally served at dinner. More expensive species are also common. Photos by Anthony Ostrowski.
Proven track record
Our company has been using the APRAS since 2011 for the culture of M. rosenbergii and other target species. Current crustacean production levels at its exiting sites in 2015 exceeded 2,500 MT, a production level that has yet to have an effect on the off-the-farm price received from the company’s SEC (U.S. Securities & Exchange Commission) filings. Having successfully completed its five-year demonstration phase, the company is now poised to expand operations with its MegaFarm project in Zhongshan, PRC.
MegaFarm project status
The project is located on 3,700 mu (600 acres) of prime agricultural land in the center of one of the world’s most highly urbanized regions in Guangdong Province, PRC, across the bay from Hong Kong. The farm will take a holistic and sustainable approach towards production. In addition to the RAS farm (targeted for Best Aquaculture Practices certification), integrated aquaponics and traditional land-based fruit and vegetable production will also be implemented using solid wastes from the farm. There will also be an integrated wetland and a migratory bird habitat.
A total 36 APRAS buildings are planned, each 7,500 square meters in size, and each containing up to 36 A-Power modules (APMs) of various sizes for each stage of grow-out. Stage 1 APM tanks are 50 cubic meters working volume; stage 2 and 3 tanks are 150 cubic meters; and final stage 4 grow-out tanks are 1,500 cubic meters. A production unit of three buildings is targeted to produce approximately 10,000 MT per year. A total of 12 production units will be built in a phased construction plan to 2024.
Top: Artist’s rendition of the MegaFarm in Zhongshan, PRC. A total of 36 buildings housing the indoor APRAS technology will be built with integrated aquaponics, vegetable and fruit farming, and a wetland with migratory bird sanctuary towards a holistic and sustainable farming approach. The Chinese Central Government has set a goal for more intensive, yet sustainable farming approaches to offset arable land loss due to rapidly expanding urbanization.
Bottom: Google map view of the MegaFarm located in the Guangdong Province north of Macau and across the bay from Hong Kong. Note location of Phase 1 (10,000 MT) with the three building production unit. Each building is 7,500 square meters. A total of 36 buildings are planned by the end of 2024.
Currently, two of three buildings of the first production unit have been completed. Test runs of the system with target species are ongoing, and we anticipate that the first set of commercial runs will begin in the fourth quarter of 2016. We plan to produce, or have in production, tanks up to 10,000 MT by the end of 2017, and up to 70,000 MT by the end of 2020.
Perspectives
The MegaFarm is arguably the most ambitious aquaculture project yet to be undertaken anywhere in the world. After years of testing and proofing, the APRAS technology is poised to become a model of sustainable aquaculture production for the 21st century. In China, with its rising middle class and increasing demand for seafood and overall food safety and sustainability, the company feels it is at the right place, at the right time, and with the right product.
References available from the author.
Có thể bạn quan tâm
Phần mềm

Phối trộn thức ăn chăn nuôi

Pha dung dịch thủy canh

Định mức cho tôm ăn

Phối trộn phân bón NPK

Xác định tỷ lệ tôm sống

Chuyển đổi đơn vị phân bón

Xác định công suất sục khí

Chuyển đổi đơn vị tôm

Tính diện tích nhà kính

Tính thể tích ao hồ