Energy efficiency in pumping systems on aquaculture farms
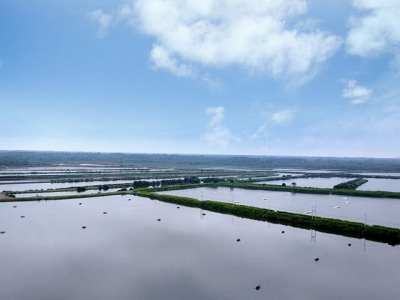
Ecuador’s sustainable strategies for improved competitiveness, production costs and maximum operational efficiency
Improving energy efficiency in Ecuador’s shrimp farming industry by increasing access to the electric grid can generate greater competitiveness, reduce production costs and help achieve maximum operational efficiency.
The current scenario of lower international prices for shrimp indicates a new reality. The growth of the world’s farmed shrimp supply – specifically from India and Ecuador, and on a smaller scale, Vietnam and Indonesia – coupled with the slow-down in demand from China and the United States have created an environment where prices will remain low, with no real forecast for this situation to change in the short term.
On the other hand, the measure announced by Ecuador’s government to increase the price of industrial diesel type 2 – the main source of energy to drive pumping and aeration systems in aquaculture farms – has generated concern, primarily because it has a direct impact on the production cost. On average, this item represents between 7 and 15 percent of the cost, depending on the efficiency of the pumping equipment and the productivity levels of the aquaculture farms, according to their specific production model.
In this scenario, the shrimp sector faces challenges, like how to be more efficient and more competitive, and how to optimize resources and reduce production costs. In this context, energy efficiency (EI) in the pumping systems of any shrimp farm – regardless of whether we are talking about a pumping system with diesel engines or electric motors – plays a strategic role with a high impact on the operational efficiency.
Fig. 1: More than one-half of the estimated 215,000 hectares of shrimp ponds in Ecuador currently have inefficient water pumping systems. Source: National Aquaculture Chamber; Delta Delfini y Cia.
According to data from the National Chamber of Aquaculture, there are around 215,000 hectares (ha) of shrimp ponds in Ecuador. According to our studies, less than 50 percent of this area have highly efficient pumping systems – these are mostly large farms of more than 250 ha. There is, therefore, a great opportunity to address and improve two structural problems of the sector that are directly linked to the energy efficiency (EI): first, to minimize the impact of the increase in diesel prices; and second, to reduce the technological gap between small, medium and large farmed shrimp producers.
Optimizing energy use in water pumping systems
Energy is the product of the power consumed (kilowatts, or kW) for a given period (hours). It is important to quantify the energy consumed, since it is what a shrimp producer pays for, regardless of whether it is from electricity or from the combustion of diesel. The quantification of electrical energy consumption is simple, because it is recorded by conventional meters that total the kW-hour consumed during a certain period, which are multiplied by the current rate.
In the case of fossil fuel energy, such as diesel, the quantification is done indirectly. The calorific value of the diesel is 37.70 kW-hour/gallon. So, what do we get for the investment in energy to power a pumping station at a shrimp farm? The answer is water.
Consequently, the key indicator to look for efficiency in a pumping system is the cost in U.S. dollars per cubic meter of water, since the concept of optimizing the energy consumption in a pumping station means obtaining the amount of water required at the lowest cost possible.
For example:
Assume that at a farm with 100 ha of pond area, the average water column is 1.10 meters; the shrimp production process requires a replacement of 15 percent of the total volume of water per day; and the farm can pump water for 16 hours, according to the historical average of tides.
Calculation of water volume to renew daily
Total volume in ponds = Vt
Vt= 100 ha x 10,000 m2/ha x 1.10 m depth = 1,100,000 m3
Volume to renew daily = Vr
Vr= 15 percent of 1,100,000 m3 = 165,000 m3
Pumping flow rate required
Pumping time per day = t
t = 16 hours x 3,600 seconds/hour = 57,600 seconds
Pumping flow rate = Qr
Number of water pumps needed
The number of pumps needed to generate the required flow rate is an operational decision. It is not convenient to have a single pump group (an assembly of engine-transmission-pump) because there will be unavoidable periods of down time of the units due to maintenance or breakdown. In this example, we will use two pumps with the criterion that if one goes out of service, the flow rate of the other will be at least 60 percent of the total flow required.
Therefore, the flow of each pump must be:
Required power of engine
The power required of the engine (diesel for this example) will vary depending on the efficiency of the pump – the more efficient the pump, the less power will be required from the engine, and its energy consumption will therefore be lower. Additionally, the height to be pumped and the system losses must be considered. In our example, we use a height of 5.5 meters.
The average power of the motors (in kW and HP) required for each pump will be:
We carried out a sensitivity analysis – based on the efficiency of the pump (n) – with three types of pumps, each with a different level of technology, and therefore efficiency. For our example, 1) 85 percent, 2) 75 percent, and 3) 50 percent.
As our example shows, as the efficiency of the pump increases, the required power of the motor decreases; therefore, the power consumption of the motor is reduced.
It is relevant to mention that most of the small and medium-sized shrimp farms in Ecuador – which account for almost 75 percent of the country’s total farms – use pumping systems with an energy efficiency of around 50 percent.
Effect on energy consumption and operating costs
Continuing with the example, if we have an average of 16 hours of pumping daily; a specific typical value for fuel consumption = (0.050 gallon/hour)/HP; and a current fuel cost = U.S. $1.17/gallon, we would have the following results shown in Table 1. It shows that for a 100-ha farm, there would be a cost overrun of approximately $70,378 per year when comparing an inefficient system vs. a highly efficient system.
Salazar, water pumping, Table 1
Pump efficiency | 85% | 75% | 50% |
Power required | 146 HP | 166 HP | 249 HP |
Diesel gallons/hour | 7.3 | 8.3 | 12.45 |
Diesel gallons/day | 116.8 | 132.8 | 199.2 |
Diesel gallons/year | 42,632 | 48,472 | 72,708 |
US$/year | $49,879 | $56,712 | $85,068 |
Cost over-run: Per pump/year | - | $6,833 | $35,189 |
Cost over-run: Per 100 ha/year | - | $13,666 | $70,378 |
Cost over-run: Per pump/5 years | - | $34,164 | $175,945 |
Cost over-run: Per 100 ha/5 years | - | $68,328 | $351,889 |
Table 1. Cost overruns in energy consumption due to inefficiency in aquaculture pumping systems.
Determining cost overrun in pumping systems
This can be determined in a practical way by measuring the following parameters for each pump:
- Actual flow rate provided by the pump (m3/sec) – the flow rate measurement can be done with a proper flow meter.
- Fuel consumption (gallons/hour). It can be done easily with a 5-gallon bucket, a scale, a stopwatch and a tachometer.
- Once the flow rate and fuel consumption are determined, the real cost of pumping can be calculated in U.S. dollars per cubic meter.
In the Ecuadorean shrimp farming industry, water pumping is a major capital investment as well as a production cost, and any efficiency improvements have significant implications for farm productivity and profitability.
Optimizing resources, reduce production costs
In addition to the savings in power and therefore the lower energy consumption (diesel in this example), energy efficiency also generates the following significant positive side effects from the point of view of operational efficiency and environmental impact:
- Lower costs of operation and maintenance of engines: fuel transport, fuel, filters, lubricants and spare parts.
- Decreased generation of hazardous waste.
- Significant reduction of greenhouse gas emissions.
- Significant reduction of noise generated by diesel engines.
Pumping of the future
The Ecuadorian government, at the initiative of the private sector, has planned the execution of an electrification plan to connect at least 100,000 ha of shrimp farms to the public electricity grid, which will allow the use of state-of-the-art equipment and technology that will support a leap in productivity and operational efficiency. From our point of view, this plan has three important benefits:
Benefits for the private sector
Currently, the price of electric energy for use by the shrimp sector in Ecuador is approximately $0.065/kilowatt-hour, a rate proposed after a comparative study of pumping costs, carried out by Aquamar S.A., Delta Delfini and GPS Group in 2016.
This study determined the equilibrium point so that the cost of pumping operations with electric motors is equal to the operating cost with diesel engines, in terms of U.S. dollars per cubic meter of water pumped. As a result, the current electricity rate became attractive, because for the shrimp sector today, it would be cheaper to use electricity instead of diesel.
Additionally, this rate – classified within the rate schedule called “agricultural and fish farming pumping” – has an hourly demand, which means that, at night, between 10 p.m. and 7 a.m., the price of electric power is close to $0.01 less per kW-hour.
Benefits for the state
The sale of electricity would have several benefits for the government, including savings in foreign exchange for diesel imports; a positive impact on the country’s economy and public finances; and a balance of payments, stability and the fiscal deficit by increasing revenues and taxes for shrimp exports.
In addition, it would bring about a multiplier effect on the country’s economy, because it would encourage private investment; the generation of employment; and demand for services and investments in electrical infrastructure, both in networks and substations, as well as in medium voltage networks within the farms.
Benefits for society and the planet
The electrification plan of the aquaculture sector of Ecuador is fully aligned with the following nine of the 17 Sustainable Development Goals 2030 of the United Nations (https://www.un.org/sustainabledevelopment/sustainable-development-goals/):
- Affordable and non-polluting energy.
- Decent work and economic growth.
- Industry, innovation and infrastructure.
- Sustainable cities and communities.
- Responsible production and consumption.
- Climate action.
- Oceans health and underwater life.
- Life of terrestrial ecosystems.
- Partnerships to achieve the objectives.
Ecuador currently has a significant opportunity to improve two structural problems of the sector that are directly linked to the energy efficiency (EI): first, to minimize the impact of the increase in diesel prices; and second, to reduce the technological gap between small, medium and large farmed shrimp producers.
Perspectives
In Ecuador, energy efficiency must move from theory to practice at the governmental level. There is an existing National Plan for Energy Efficiency that has still not reached the aquaculture sector. To ensure it does, it is necessary for the state to design and implement concrete and tangible tools and incentives: the interest of multilateral organizations, international cooperation agencies, and banking in general. The plan presents an excellent opportunity for small and medium producers to access green credit lines that allow them to invest in highly efficient pumping systems, and for specific tax incentives to be added to these credit lines from entities such as the Ministry of Environment and its Punto Verde (Green Dot) program.
The current scenario has a sense of urgency both from the private sector and the public sector, to design and implement a long-term strategic agenda with three approaches: 1. To improve the competitiveness of the Ecuadorian shrimp sector; 2, To achieve fiscal balance; and 3. To continue positioning and differentiating the Ecuadorian shrimp as the best in the world, not only because of its quality and taste, but also for its sustainable production model.
We applaud the private initiatives like the Sustainable Partnership Program (SSP) led by the National Aquaculture Chamber in Ecuador, where we see opportunities to join forces in order to collaborate and complement this vision of sustainability.
The electrification program is undoubtedly one of the solutions to the structural problems of the shrimp farming sector in terms of competitiveness. However, there are several bottlenecks that the state still has to resolve, including among the most relevant ones: 1. Price certainty for electric power in the long term; 2. A regulatory framework that allows financing the electric networks and substations under the Public-Private Partnerships model; and 3. Specific financing with competitive rates and terms.
Aligned with this vision, the GPS Group and Aquamar have launched the private initiative AQUA 2.0® (La Acuacultura del Futuro®), aiming to accelerate the electrification and technical advancement of the shrimp farming industry in Ecuador. This private initiative has been supported by local and world class technical suppliers like Delta Delfini, Cargill – iQuatic, Siemens, Orca Tecnologías, and major shrimp farm players in Ecuador.
Có thể bạn quan tâm
Phần mềm

Phối trộn thức ăn chăn nuôi

Pha dung dịch thủy canh

Định mức cho tôm ăn

Phối trộn phân bón NPK

Xác định tỷ lệ tôm sống

Chuyển đổi đơn vị phân bón

Xác định công suất sục khí

Chuyển đổi đơn vị tôm

Tính diện tích nhà kính

Tính thể tích ao hồ