KnipBio partners with ICM to scale-up production of single-cell protein for aquaculture
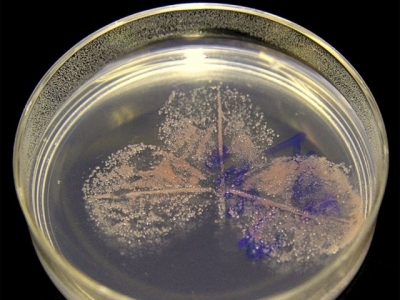
Partnership with leader in fermentation, bio-refining will enable tenfold increase in production of KnipBio Meal
KnipBio’s single-cell protein technology is based on the leaf symbiont Methylobacterium extorquens. The microbe’s metabolic versatility translates to tailored nutritional solutions. Photo courtesy of KnipBio.
Biotechnology company KnipBio has entered into a joint development agreement (JDA) with ICM, Inc. to scale up production of KnipBio Meal, a single-cell protein product, or microbial meal, that is a nutritious aquaculture feed ingredient.
Larry Feinberg, CEO of KnipBio, told the Advocate that ICM – recognized as a worldwide leader in corn ethanol production, fermentation and bio-refining technology – is a “great strategic fit.” ICM has vast expertise in engineering, design and procurement that will fuel KnipBio’s transition from its R&D laboratories in Lowell, Mass., USA, toward commercial production.
“Bringing together ICM’s best-in-class fermentation know-how and KnipBio’s innovative biotechnology will allow us to dramatically accelerate our commercial plans,” Feinberg said. The deal represents rapid, capital efficient path toward achieving an “order of magnitude” increase in production capacity, from 20,000-liter vessels to 200,000 liters.
“Aquaculture needs new sources of traceable, sustainable and resource-efficient protein,” said Steve Hartig, ICM’s VP of technology development, in a prepared statement. “We believe KnipBio’s premium single-cell protein technology could play a central role in meeting this need. Alternative proteins for aquaculture will be a multi-billion-dollar market and this process enables the U.S. ethanol industry new opportunities for growth.”
Feinberg, who established a relationship with ICM during his previous ventures in biofuels before moving on to aquafeed protein production, said the time is right for ICM to explore new manufacturing opportunities, given the global pivot away from biofuel production and potential trade barriers that may drive further market shifts for manufacturers.
“ICM enabled the corn-ethanol industry. They streamlined and made the industrial process very efficient and simple,” he said, adding that ICM presented a long “checklist” of positive attributes that led to the JDA, which is expected to last for one year.
While there are differences regarding the specifics of ethanol and the single-cell protein fermentations, Feinberg said the concepts are essentially the same. KnipBio Meal will be manufactured at ICM’s pilot plant in St. Joseph, Mo., USA.
ICM has provided proprietary process technology to 106 facilities globally, establishing itself as a leader in bio-refining technology. Partnering with a company with that level of knowledge increases KnipBio’s chances of success, said Feinberg.
Inside a 20,000-liter fermenter used to produce KBM through the company’s dedicated fermentation process. This type of equipment offers a very high degree of process control and is relatively standard equipment.
“They have an amazing ‘shop’, it’s like being a kid in a candy store for a microbiologist like me! Their processing equipment, pre-commercial scale large reactors, analytical equipment different-sized bioreactors, and talented personnel will more than meet our needs for the commercial development of our products,” he said. “If I were to reconstruct this, it would cost many tens of millions of dollars. There’s a long track record of companies trying to do everything on their own. And in doing so, there’s often such a high level of risk that there’s near certainty of failure. Leveraging ICM’s knowledge, expertise, equipment and resources to address and attack one of the things that we need to prove – scaling up – gives us better odds of success.”
KnipBio’s bacterial strain and biotech development will remain in Lowell, with processing and scale-up occurring in Missouri. Feinberg said this JDA is an important step on the company’s “march toward commercialization.”
Aquaculture needs new sources of traceable, sustainable and resource-efficient protein.
The company is currently working on “half a dozen” trials on four continents with commercial aquaculture outfits to gauge the effectiveness of KnipBio Meal in aquafeeds. Each of these commercial partners has, according to Feinberg, “an appetite for innovation.”
“The vision is to seed the market now for the next phase,” said Feinberg, touting the immuno-nutritional properties of the single-cell protein, which can be customized for species’ nutritional requirements. The company announced earlier this year that it had developed a meal containing a bio-astaxanthin carotenoid that shrimp, salmon and trout producers could deploy in feeds to give their products’ flesh the red-orange-pink hue that consumers have come to recognize and place a high value on.
Feinberg said ICM recognizes the potential of KnipBio’s PROTEINplus product strategy, and the investment is validation of the research his company has conducted over the past three years.
“This is not just a protein, but a way to make healthier animals, with fewer demands on antibiotics and a greater resistance to disease,” he said. “The idea is not just to feed, but to give the animals the right food, with the right compounds that stimulate the immune system. Aquaculture is just beginning to figure this out.”
Có thể bạn quan tâm
Phần mềm

Phối trộn thức ăn chăn nuôi

Pha dung dịch thủy canh

Định mức cho tôm ăn

Phối trộn phân bón NPK

Xác định tỷ lệ tôm sống

Chuyển đổi đơn vị phân bón

Xác định công suất sục khí

Chuyển đổi đơn vị tôm

Tính diện tích nhà kính

Tính thể tích ao hồ