Rising use of automatic feeders in shrimp ponds poses new feed requirements (Part 2)
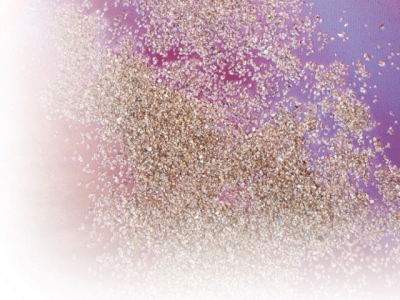
Particle homogeneity: diameter and length
Feed homogeneity, in terms of diameter and length, is directly related to its utilization. Homogeneity in feed particle size ensures that after capture, the most is made of the feed particle.
Feed size and its influence on feeding has been reported by Obaldo and Masuda (2008), who investigated six diet sizes and their effect on the feeding behavior and growth of juvenile Pacific white shrimp (Litopenaeus vannamei). The results indicated that when shrimp are fed with larger pellets, some of the individuals monopolize the feed and obstruct the feeding behavior of others, and this is significantly different between feed sizes. This shrimp behavior was observed with greater frequency in shrimp fed with 3.0 mm pellets, in comparison to shrimp fed with 0.7 and 1.2 mm pellets, which could result in a considerable variation in size and mortality of the smallest individuals.
From the point of view of the mechanical flow inside hopper, pellet diameter and length play a critical role, because the degree of packing of more homogeneous particles leads to a balance of forces that improves flow.
Fig. 2 shows the frequency distributions of the lengths, with significantly lower standard deviations in certain feeds. Note that diet D has a symmetric distribution (an almost perfect bell distribution), while the other diets – A, B, C, E and F – have less homogeneous distributions.
Fig. 2: Frequency distribution of the length of various manufactured aquafeeds for shrimp.
Product homogeneity means a more balanced access to the feed for all animals during conditions of high animal density of animals, typical of feeding areas around a feeder. Mechanically, this also translates into a more uniform and uninterrupted flow, which allows the feeder to dynamically dispense the programmed quantities.
Fines
The fines in the feed constitute losses because they are not used by the animals, and in fact, their decomposition affects water quality. In automatic feeding, the transfer of feed from the feed mill to the shrimp farm warehouse and later to automatic feeder hoppers generate a greater or lesser amount of fines depending on the type of feed.
During transport, while in storage and when dispensed, the mechanical forces that come into play make poorly manufactured feed even more prone to disintegration, with the consequent increase in feed particles that will not be utilized by the cultured animals (Fig. 3A). The accumulation of these fines blocks the exit holes, preventing the normal projection of the feed pellets during automatic feeding. This type of obstruction is even more severe in feeders with V outputs (Fig. 3B). This type of feeders, having exit holes with a small dispensing surface, can become clogged with feed pellets combined or mixed with fines.
Fig. 3: Fine accumulations in the floating tanks of an automatic feeding system (A); feed blockage in a type V dispenser – note the amount of fines generated around it (B).
Table 2 shows several physical parameters of the feed that are directly related to the performance of the automated feeder. An interesting case is related to the humidity of the product. Above the range mentioned in Table 2, specifically at a humidity of 11.8 percent, a greater tendency for blockages is observed due to lumping. The lumps obstruct the outputs of the feeder, preventing normal feed projection and distribution.
Molina, feed characteristics, Table 2
Parameter | Valyue |
Pellet harness (kg f/cm2) | 1.1 – 1.8 |
Fines (%) | up to 0.3 |
Durability index (%) | 98.2 – 99.7 |
Coefficient of variation of length (%) | 9.5 – 20.0 |
Density (g/mL) | 1.16 – 1.21 |
Coefficient of variation of diameter (%) | 4.7 – 6.9 |
Moisture (%) | 9.8 – 11.15 |
Pellet volume (mm3) | 3.6 – 19.0 |
Table 2. Physical parameters of manufactured aquafeeds observed to not interfere with automatic feeder performance.
With higher levels of humidity, such as 12 percent, the greatest problems with blockages due to lumps have been reported – up to 5 blockages when dispensing a 25 kg bag of feed. For this reason, external liquid addition to the feed prior to distribution by automatic feeder is not recommended due to the caking effects that have been observed in tests when adding various liquids to the feed after its manufacture.
Conclusions
The introduction of automatic feeding systems generates the need to improve the physical quality of aquafeeds. At the same time, it is necessary to adapt these systems to a new reality where the feed properties determine, to a large extent, the performance of the equipment and, ultimately, the feeding strategy. On the other hand, the physical and design characteristics of the feeder also directly affect performance.
The interactions of solids, understood as flows and jams, are complex. In specific environments such as in aquaculture production, the physical-mechanical properties of aquafeeds have particularities that merit attention due to a number of possible issues. The relative humidity, storage time, the level of the material, and feed humidity and temperature are other variables that are in play and that have been studied only superficially. Therefore, more studies are necessary in order to mitigate any issues created and to better understand the guidelines governing their behavior.
The distribution of feed through automatic devices presents multiple challenges that are closely related to the type of food, size, shape, dispensing speed, range and others. All of these are physical characteristics that determine the performance of the feeder and ultimately, make the difference compared to a traditional feeding strategy.
The characteristics, both of the feeder and of the feed, that lead to a feeder failure or blockage are related in one way or another to the forces of compaction and friction. Minimizing these issues using devices that reduce the force on the bottom of the hopper should be done and monitored in such a way that the designed feeding program can be implemented to achieve the best possible performance.
References available from first author.
Có thể bạn quan tâm
Phần mềm

Phối trộn thức ăn chăn nuôi

Pha dung dịch thủy canh

Định mức cho tôm ăn

Phối trộn phân bón NPK

Xác định tỷ lệ tôm sống

Chuyển đổi đơn vị phân bón

Xác định công suất sục khí

Chuyển đổi đơn vị tôm

Tính diện tích nhà kính

Tính thể tích ao hồ