Shrimp biofloc production trials in Saudi Arabia
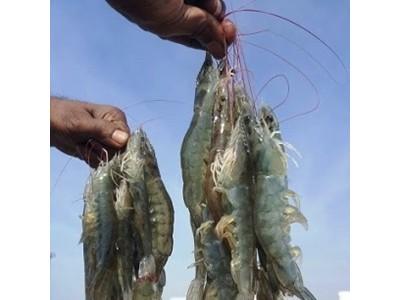
Getting results in a challenging desert environment
Shrimp harvested at the end of the RSACO trial.
The desert climatic conditions of the Kingdom of Saudi Arabia (KSA) present a challenging environment for the implementation of shrimp biofloc production technology. Shrimp farms in the region — just like those in Asian and South/Central American countries — have had their share of disease issues, and KSA shrimp farms switched shrimp species in 2013 from the native Indian white prawn (Penaeus indicus) to Specific Pathogen Free (SPF) Pacific white shrimp (Litopenaeus vannamei). The production systems implemented were extensive flow-through in very large ponds and producing 2.5-4.0 mt/ha/cycle of shrimp (L. vannamei). A few experimental trials in small ponds were also carried out at King Abdul Aziz University, Jeddah with L. vannamei in biofloc system with promising results, achieving around 20 mt/ha/cycle.
The latest R&D trials reported here with a L. vannamei biofloc system was the outcome of an FAO project (“Strengthening and supporting further development of aquaculture in the Kingdom of Saudi Arabia” — UTF/SAU/048/SAU). The project’s objective was to train the researchers at the Jeddah Fisheries Research Centre (JFRC) in commercial biofloc aquaculture techniques; preparation of a field handbook for aquaculture biofloc systems suitable for the desert climatic conditions of KSA; and to develop a scientific project proposal for joint collaborative research between JFRC and a selected research institution. One of us (NT) was FAO consultant for the project in May 2014 and conducted a shrimp biofloc workshop at the JFRC for its technical staff and other interested, private sector investors and technicians, researchers and other aquaculture stakeholders. The subjects covered essential topics for application in shrimp commercial farming in biofloc technology.
Here we present the results of an R&D trial with biofloc technology at a commercial facility, Red Sea Aquaculture Co. (RSACO), prior to it initiating a much larger scale project based on these results.
Trial setup
The RSACO shrimp farm is located in Jizan, on the southwestern Red Sea coastal area of KSA (Fig. 1). Four small R&D trial ponds were constructed following a standard protocol for biofloc system culture (Fig. 2). The 25 x 35 x 2.2-m ponds were fully lined with HDPE liners and equipped with a central drain system. Surface area of ponds was 0.0875-m2 and water volume was 1,925-m3. Two, 3-hp “Force 7” air-injector aerators were used in each pond at opposite sides to create a smooth water current flow. This circular current created and maintained homogenous water columns, clean pond bottoms and accumulated the sludge towards the ponds’ center drains, all ideal for shrimp biofloc systems.
The RSACO shrimp farm where the trial was conducted is located in Jizan, on the southwestern Red Sea coastal area of KSA. Arrow points to location where the four trial ponds were built and operated.
Operation and control in biofloc system
Four small R&D trial ponds were built and operated following a standard protocol for biofloc system culture of shrimp.
In general, standard shrimp biofloc operations were followed, but due to extreme environmental conditions with very high salinity and temperatures because of the Red Sea water used, the system was adapted to suit these environmental conditions. Shrimp (L. vannamei) postlarvae (PL) were purchased from the National Aquaculture Group (NAQUA group). SPF PL21 (21-day old postlarvae) were stocked directly into the trial ponds. All ponds were stocked on the same day at a density of 51.5 PL/m3.
Ponds were filled to maximum depth before stocking. For the first 60 days of the trials, no water was exchanged. At this time, pond water salinity had increased to close to 51.0 ppt, so from that time on pond water was exchanged at 10-30 percent every 2-3 days to keep the water salinity lower. A standard feeding protocol based on estimated biomass plus feeding rate was applied, but it was also adjusted results of daily feed tray monitoring.
During the initial 60 days of culture, standard biofloc practices were used including applications of wheat flour and molasses to the pond water to promote heterotrophic bacteria. Wheat flour at 10-20 percent of daily feed quantity was added from day 1. Molasses was applied at 10-20 ppm separately with/without brewing with bakers’ yeast in quantities adjusted to wheat flour amounts used. After 60 days, the pond system was shifted to a semi-biofloc protocol by adding 10-20 percent wheat flour in daily feed rations and also molasses to control ammonia build up and to control indigenous heterotrophic bacteria. Sludge accumulated in the center of the ponds was regularly removed through the central drains.
Each trial pond had aerators at opposite sides to create a smooth water current flow, maintain dissolved oxygen levels and accumulate sludge in the center for removal.
Pond water exchanges were done every 2-3 days depending on water turbidity and color, or when salinity was on the rise. The main reason for pond water exchange was to maintain salinity within 44-45 ppt. Biofloc volumes at <5.0 ml/L) or Secchi disk readings of 15.0 cm were also maintained. Changes in pond water color during the trial were from green to brown to coffee- brown in a cycle of three weeks. Foaming was noted almost every day, but more in the first day of applications of molasses and wheat flour. Due to demand for large size shrimp, the culture period was extended to 152 days.
The pond water environmental conditions during the trial, if compared to similar technology systems in Asia, were considered to be extreme in terms of salinity and temperature. The salinity was maintained at between 42.0 and 49.5 ppt during the culture trial period. Other essential water quality parameters during the trial included water temperatures of 26.0 – 35.0oC; pH 6.7 – 9.2; dissolved oxygen (DO) levels > 3.7; alkalinity 70 – 150 ppm; TAN 0 – 0.5 ppm; water transparency 9 -134 cm with biofloc levels of 2 – 3 ml/L.
Production performance
The performance data for the R&D trial runs are shown in Table 1 and Figure 4. The trial was a success, but as expected and anticipated, the standard biofloc protocol had to be adapted to suit the extreme desert, Red Sea environmental conditions – high salinity and temperature.
Taw, Table 1
Pond | Area (ha) | Stock density M3 | DOC | Harvest kgs per pond | Kg/ha projected | ABW-gm | AWG-gm | Survival % | FCR | Aeration efficiency kg/hp |
SP1 | 0.0875 | 51.5 | 141 | 1,400 | 16,000 | 24.39 | 0.17 | 64 | 2.1 | 233.33 |
SP2 | 0.0875 | 51.5 | 141 | 1,850 | 21,143 | 23.26 | 0.16 | 88 | 1.85 | 308.33 |
SP3 | 0.0875 | 51.5 | 141 | 1,830 | 20,914 | 23.26 | 0.16 | 87 | 1.91 | 305.0 |
SP4 | 0.0875 | 51.5 | 152 | 1,875 | 21,429 | 27.78 | 0.18 | 75 | 1.92 | 311.67 |
Results data for the RSACO R&D trial runs for the four ponds used.
Fig. 4. Growth of shrimp (L. vannamei) during the trial at RSACO’s small ponds.
The results were as good as the results from semi-biofloc systems in Malaysia, with production of over 20 mt/ha with shrimp size range of 23.6 to 27.78-g in 141-152 days of culture. Shrimp growth per day was also standard, between 0.16-0.18 grams. The Feed Conversion Rate (FCR) was higher, however, and this could be due to significant rates of pond water exchange to keep pond water salinity within acceptable limits below 50.0 ppt. Survival was mostly as good as in Malaysia, except for one pond that was below standards. The aeration efficiency was much lower than the Malaysia standard, possibly related to the very high water salinities and temperatures, and needs to be addressed.
A comparison between the RSACO trial and Malaysia biofloc systems is provided in Table 2. Our results indicated that biofloc technology can be effectively applied, with some protocol adjustments, in the KSA’s extreme desert environmental conditions. Promising results were also observed from a few experimental trials in small ponds carried out at King Abdul Aziz University, Jeddah with Pacific white shrimp in biofloc systems. A biofloc system with additional substrate in 1,000-m2, HDPE-lined ponds produced 20 – 22 mt/ha (projected) in 13 weeks using unselected Ecuadorian stocks of SPF L. vannamei. In another trial, 300m2 HDPE-lined, shaded, biofloc ponds achieved an average projected production of 19 mt/ha in 14 weeks. Both trials used nursed shrimp PL before stocking in the trials ponds.
Taw, Table 2
Parameter | RSACO Trial (KSA) | Malaysia |
Production (MT/ha) | 16.0-21.4 | 14.0-16.0 |
Feed conversion ratio | 1.85-2.1 | 1.3-1.5 |
Culture period | 141-152 | 100-105 |
Biofloc volume (ml/L) | 2-3 | <5 |
Size at harvest (g) | 23.26-27.78 | 18.0-20.0 |
Energy efficiency (kg/hp) | 233-312 | 540-712 |
Water exchange | As necessary after 60 days | Zero (topping up only) |
Culture water salinities (ppt) | 42.0-49.5 | 25.0-30.0 |
Culture water temperature (degrees C) | 26-35 | 26-30 |
Comparison performance between RSACO trial ponds and a typical Malaysia semi-biofloc system.
Perspectives
In general, the results of our R&D trial and other similar results from experimental trials at King Abdul Aziz University suggest that implementing biofloc technology is feasible for shrimp production in the desert environmental conditions of the Kingdom of Saudi Arabia.
Author’s note: references available from Dr. Nyan Taw.
Nyan Taw Ph.D.
Consultant – Shrimp Aquaculture Technology (Former GM, Blue Archipelago BHD, Malaysia and CTA of FAO Projects of the UN)
Radhakrishnan Palasseri M.Sc.
Site Operation Manager Red Sea Aquaculture Co. (RSACO), Jizan, Kingdom of Saudi Arabia
Ziyad Ahmad AlRahmah
Certified Consultant, Industrial Management CEO, RSACO and Vice President (Saudi Aquaculture Society)
Periyathambi Sampath M.Phil.
Shrimp Consultant, Jeddah Fisheries Research Centre, Ministry of Agriculture, Jeddah, Kingdom of Saudi Arabia
Có thể bạn quan tâm
Phần mềm

Phối trộn thức ăn chăn nuôi

Pha dung dịch thủy canh

Định mức cho tôm ăn

Phối trộn phân bón NPK

Xác định tỷ lệ tôm sống

Chuyển đổi đơn vị phân bón

Xác định công suất sục khí

Chuyển đổi đơn vị tôm

Tính diện tích nhà kính

Tính thể tích ao hồ