Thinking outside the cage: Avant-garde aquaculture in Norway
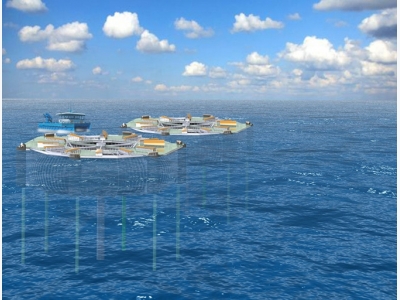
With designs on the drawing board and other technologies already in the water, salmon farming is poised for an innovation boom
An artist’s rendering of the donut-shaped enclosures designed by OPD Group.
Nils-Johan Tufte dreams of swimming salmon. Not in some remote mountain river, but in a continuous loop against an adjustable current within a giant, donut-shaped thermoplastic enclosure built by his company OPD Group, a marine contracting firm in Norway.
These space-aged structures could provide a controlled, contained environment to optimize existing salmon farm sites in fjords and near-shore areas that dot the Norwegian coastline, said Tufte. He hopes the innovative design will help the salmon farming industry solve persistent problems like sea lice, disease, fish escapes and waste management.
He’ll know by October, and possibly sooner, when the Norwegian government is expected to announce special development license approvals for forward-thinking companies that have applied for them.
The donut design by OPD – which specializes in high-density polyethylene (HDPE) pipelines and tanks in marine environments – is among 34 applications awaiting permission from the Norwegian government to be put in the water to test. Each application represents a concept or technology and can involve multiple licenses. Companies calculate the estimated fish volume for their concept and apply for a license for every 780 metric tons of fish.
“If we can start building it this fall, that would be great,” said Tufte, CEO of OPD Group, which would build five donuts for Marine Harvest and install them by 2018 off the coast of Nordland, a county in northern Norway where the world’s largest farmed salmon producer already operates a facility.
The aquaculture industry needs to innovate and be more sustainable if we are to grow in the future and meet the demand in the markets.
At 55 meters, the width of each donut is roughly half the length of a football pitch. Each structure weighs 370 metric tons and holds 22,000 cubic meters.
The shape is cost-effective for the HDPE material, which can withstand harsh marine weather conditions, be recycled and safely contain the salmon inside, said Tufte. The entire system can be buttoned up to contain a problem like disease or to keep out a problem like an oil spill in local waters. In that event, oxygen can be added for the fish and farmers, said Tufte.
Additionally, the water temperature can be adjusted, and waste materials can be collected and recycled or treated in a bioreactor to reduce nutrients by 30 to 40 percent before discharge.
“The obvious advantage of the donut is that it is a closed system, keeping the fish and the surrounding environment separated,” said Ola Helge Hjetland, communications manager at Marine Harvest, which is weighing a number of new production technologies. “That will hopefully lead to healthier fish and a smaller environmental footprint. Reduced need of treatment will also lead to reduced costs.”
Seeking a successor to the cage
Marine Harvest has applied for 34 of these development licenses, spanning four different new technologies or concepts. Three are contained systems — the donut, The Egg from Hauge Aqua (see link below) and farms on cargo ships — and the other a structure that allows salmon farming in more exposed marine sites.
In fall 2015, the Norwegian government offered over a two-year span an unlimited number of these special development licenses to help reduce the risk and cost of trying new technologies that can solve environmental problems and to expand the industry.
A 2015 white paper from the Norwegian government detailed environmentally sustainable, potential growth in the country’s salmon and trout farming, looking ahead to 2050. The researchers estimated the growth potential in the Norwegian seafood industry to be six-fold, mostly within salmon farming. The white paper was based in part upon this study.
“The Norwegian government uses development licenses as an incentive for the industry to find new and more sustainable ways to farm salmon,” said Marine Harvest spokesman Hjetland. “We believe this is a wise initiative. The aquaculture industry needs to innovate and be more sustainable if we are to grow in the future and meet the demand in the markets.”
Innovation doesn’t come cheap
Ocean Farming AS, a subsidiary of the SalMar Group and supported by Kongsberg Maritime AS, won approval to build the world’s first automated “exposed” aquaculture facility.
At a cost of 65 million NOK ($7.8 million) for each donut, the Marine Harvest project represents a 325 million NOK ($39 million) sale for OPD Group and a strong foothold in a new market. If the donut concept over the next 15 years solves environmental and siting problems to the satisfaction of the Norwegian government, Marine Harvest stands to save at least 250 million NOK ($30 million), when it converts those development licenses to commercial ones — easing the cost and risk of its research and development effort.
Marine Harvest declined to specify its typical or recent spending on research and development. “If the applications are approved, the production of these pens will of course be significant investments for the company,” said Hjetland.
To win approval, a project must represent significant investment and innovation toward solving environmental problems and issues related to location — meaning it must be easier to manage in a coastal area or it works in a new type of site.
Once approved, the government will set specific criteria for that project to meet, said Mari Sorensen Aksnes, a legal advisor in the department who works with applicants and writes the decisions. The manufacturer and salmon farming companies must have a plan to share the technology with the industry, she said, for the greater good.
Reduced need of treatment will also lead to reduced costs.
So far, officials in the Aquaculture and Coastal Management Department in the Norwegian Directorate of Fisheries have approved one application and denied four, said Sorensen Aksnes.
Ocean Farming AS, a subsidiary of the SalMar Group and supported by Kongsberg Maritime AS, won approval to build the world’s first automated “exposed” aquaculture facility. The project combines technologies from the Norwegian aquaculture, and offshore oil and gas industries. The design calls for a submerged, anchored fixed structure that floats in the exposed ocean at depths of 100 to 300 meters, according to a press release from Kongsberg Maritime.
Conditions at such exposed sites, up to several miles offshore, boast steady currents that limit exposure to sea lice infestation and benefit the health of the fish, according to Kongsberg. The facility is designed to be fully automated, requiring a crew of three to four people. It can also be remotely operated, according to Kongsberg.
Continuous improvement in cage techniques
Innovative techniques and technologies can of course be found in more traditional net pen structures.
One of Marine Harvest’s top competitors, Cermaq, has introduced iFarm, a new system developed by BioSort AS that employs a visual technology to recognize individual fish based on their dot patterns.
In an iFarm system, the fish are channeled into a sensor chamber that registers size, presence of sea lice and possible signs of disease. The system can detect any changes in a fish’s growth rate, which allows diagnostic work and treatment to start earlier, according to a Cermaq online release.
Individual fish can be removed for lice treatment, reducing the use of broadcast treatments.
“This is a technological leap for the cage-based salmon farming, where we shift from group-based operations to individual registration and treatment,” said Cermaq CEO Geir Molvik. “iFarm will be a significant contribution to the solution of the area challenges that aquaculture is facing.”
Cermaq has applied for 10 development licenses to take iFarm from the concept phase to commercial implementation.
As new approaches to salmon farming hit the water, the question becomes: Will these solutions work in other countries?
“We have reasons to believe this will work [elsewhere] as well,” said Tufte of the donut. He hopes to build the structures in local shipyards, should that come to fruition.
Also in Tufte’s dreams? Harnessing and storing renewable energy on fish farms, creating an additional revenue stream for operators or, at the very least, powering their donut-shaped cages using the sun, wind and waves.
Có thể bạn quan tâm
Phần mềm

Phối trộn thức ăn chăn nuôi

Pha dung dịch thủy canh

Định mức cho tôm ăn

Phối trộn phân bón NPK

Xác định tỷ lệ tôm sống

Chuyển đổi đơn vị phân bón

Xác định công suất sục khí

Chuyển đổi đơn vị tôm

Tính diện tích nhà kính

Tính thể tích ao hồ