Tools for litter management in cage-free layer houses
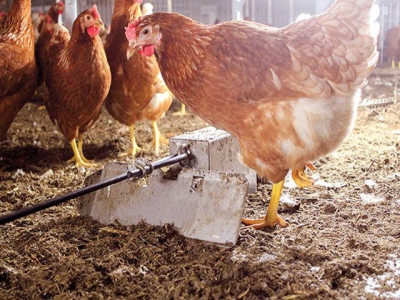
Litter scrapers, like the top pivot one, can be used to keep litter depth at no more than 1 inch to control ammonia and dust in a cage-free layer house. | Photo courtesy of Jansen Equipment Company
Controlling litter moisture and depth in cage-free aviary systems are important for maintaining air quality and bird health.
“The key to success for cage-free egg production is a manager who is open-minded and interested in learning,” said Steve Walcott, Big Dutchman's vice president of sales. “We can’t just take what we know about traditional housing and expect those practices to work in cage-free production. We need to develop a new set of skills to keep all the moving parts working together properly.” It is important to add litter management to the growing list of responsibilities for cage-free production managers. Walcott added, “Producers are spending a lot of money on litter management.”
The litter area under an aviary system and/or in the walkway plays an important role to meet animal welfare requirements. Besides providing additional space, the litter area is used by birds for dust bathing, foraging and scratching, which help reduce picking and cannibalism. Also, dust bathing helps maintain optimal feather condition, improving the birds’ ability to regulate body temperature.
Optimal litter conditions and depth
Producers strive to ensure litter is dry and friable (easily crumbled) with management measures such as humidity control, ventilation and litter amendments, if necessary, as well as specially designed equipment.
Managers strive to prevent high litter moisture levels (over 20 to 25 percent) that result from the litter and manure mixture caking, which increases the likelihood of ammonia problems. Likewise, extremely dry conditions result in an increase of particulate matter (dust) and bacteria load in the house, which can affect bird and worker health. (For further discussion, see this article in the April 2018 issue of Egg Industry)
Research has shown that optimal litter depth to keep ammonia and dust at acceptable levels is 1 inch. Even just another inch (2 inches total) of litter has been shown to increase ammonia and dust by 25 percent. Deeper litter also encourages birds to nest and lay eggs on the floor, which increases food safety risks and labor costs required for manual egg collection.
Litter reduction and scraper systems
Litter reduction systems (floor scrapers) are an important design feature in aviary housing that have proven successful in European layer operations over the past 10 years. Teus van Harskamp, product engineer at Jansen Poultry Equipment, explained: “The scrapers have two purposes — first to remove litter in order to minimize ammonia and dust, and second, to reduce floor eggs.”
The scraper systems are generally set up about 15 feet apart under the aviary system across the width of the house. Cables run the length of the building and have multiple scrapers attached, which are spaced a bit less than the run length. A drive unit moves the scrapers both forward and backward with a run up to 25 feet. The next scraper moves the accumulated litter forward that was left by the previous scraper. Litter is ultimately moved to a conveyor for removal.
Litter scrapers can be used to move excess litter to the end of the house where it is carried out of the building on a manure belt. | Photo courtesy of Jansen Poultry Equipment
Only small amounts of litter are actually removed when the scrapers are run. As additional manure from the birds dries and becomes part of the litter mixture, usually there is not a need to replenish the litter. The birds move litter back into areas cleaned by the scraper, helping distribute litter evenly across the house.
There are some design differences offered by equipment manufacturers. The scrapers have a pivot point attached to the cable, which allows the blade to be moved both forward and backward. The pivot point may be designed at the top of the blade to minimize plugging. Other designs have folding wings, which fold when moving in reverse. Some manufacturers offer varying widths of scrapers suggesting wider scrapers at the end of the cable line.
Some litter scrapers, like this one manufactured by Geerts Smederij, have arms or “wings” that fold together when the scraper is pulled backwards, but fold out when pulled forward to move litter to a manure belt at the end of the house. | Photo courtesy of Vencomatic
In order to discourage birds laying eggs on the floor, some manufacturers recommend running the scrapers back and forth during the early morning lay period. Equipment manufacturer recommendations vary on the frequency of running the scrapers for actual cleaning purposes. Based on experience with their particular aviary design, some prefer cleaning small amounts daily, while others may suggest only once every four days when the manure belts run.
Adaptations required and potential challenges
As U.S. producers continue building aviary systems, they are also incorporating this equipment as appropriate for the house design. However, there are some adaptations required due to the size of the houses. Cage-free farms are being built in the U.S. with 200,000 to 400,000 birds or more under one roof.
Walcott noted: “The current trend is using litter reduction systems on the concrete first level floor where birds have access to litter under the aviary system. On second and/or third floor levels, solid walkways are used for litter access. Under the aviary system, wire mesh floors and takeaway belts are being utilized to assist in manure and litter management.”
Managers are still seeking efficient ways to manage the litter on the walkways of the upper levels without the benefit of floor scrapers. The birds move the litter quickly, and frequent replenishment becomes a labor and cost issue. Another potential challenge resulting from the use of this design might be behavioral issues from less available litter space for dust bathing and foraging. As producers and managers gain more experience with aviary housing in the U.S., they will continue to work with equipment manufacturers to improve designs and optimize management practices.
About Author:
Jerry Dreyer has worked in the poultry industry in global marketing and sales roles in animal health and genetics companies. He now assists clients with market and product development, communications, research and marketing projects.
Có thể bạn quan tâm
Phần mềm

Phối trộn thức ăn chăn nuôi

Pha dung dịch thủy canh

Định mức cho tôm ăn

Phối trộn phân bón NPK

Xác định tỷ lệ tôm sống

Chuyển đổi đơn vị phân bón

Xác định công suất sục khí

Chuyển đổi đơn vị tôm

Tính diện tích nhà kính

Tính thể tích ao hồ