An engineers design for a classroom aquaculture-aquaponics system
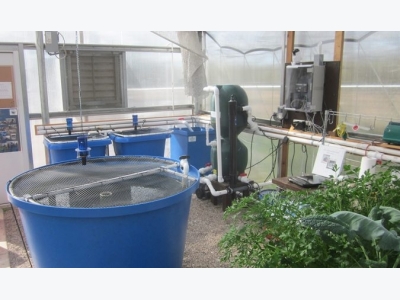
Interest and investment in the technology is growing
Aquaculture system showing three production tanks, pump sump, Bubble washed-bead filter, automatic feeders and monitoring system.
Aquaponics – the integration of aquaculture and hydroponics – continues to gain attention because it offers the opportunity for localized, sustainable, small-scale production of both fish and vegetables. Aquaponics utilizes the nutrient-rich water from aquaculture production of fish as a source of nutrients for growing plants and vegetables. In a public-school setting, an operational greenhouse provides great educational opportunities as well as producing healthy and delicious food for the students.
Growing interest in local food production
Over the past few years, the United States has seen an incredible growth in interest and investment in aquaponic systems. Numerous conferences, workshops and short courses are being offered to introduce both commercial investors and small-scale urban and community growers to this integration of hydroponics and aquaculture, i.e. plants and fish.
This increased attention to aquaponics is primarily due to a renewed interest in growing food locally under controlled conditions, free from pesticides, herbicides and other chemicals used in more traditional agriculture. Although aquaculture has been included in many school curricula over the past decades, only recently has the growing of plants, usually leafy greens, been added as a secondary crop. Aquaponics utilizes the nutrient-rich water from aquaculture production of fish as a source of nutrients for growing plants and vegetables.
Education and training
As this industry starts to mature, one of the most important components needed for its success is experienced and trained staff to manage and operate these endeavors. Currently there are few programs that offer education and training in aquaponics. In addition, most secondary schools have limited resources for the design and construction of aquaponic teaching systems.
To help overcome this limitation, the Agriculture & Biosystems Engineering senior capstone students at the University of Arizona were asked to design and implement an aquaponics system for an on-site, underutilized greenhouse (7.6 x 15.25 meters) with the goals of producing food for the cafeteria and integrating its operation and management into the educational curriculum.
Two of the primary goals of this project were to design a small school aquaponics system using basic engineering design principals, and to construct a professional-looking system that the school, students, and community could be proud of. This turned out to be an excellent example of engaging engineering students in a real-world design problem and provided the school with a system that will be integrated into several curricula and provide training for at-risk and challenged students.
Media bed with an expanded clay media growing herbs, strawberries and tomatoes.
Engineering perspective
From an engineering perspective, a small-school system has the same design criteria as a larger system, only with less production volume. In addition, some components can have dual purposes, thus saving on the initial investment costs. Breaking the system down into a recirculating aquaculture system and a hydroponic system allows for two separate designs with the option of operating them linked together or, if necessary, separately.
Engineers like to divide complicated systems into small parts, called “unit processes” that correspond to a specific treatment process. A recirculation system can be subdivided into seven individual unit processes that may correspond to separate systems or be linked together in a process stream. These unit processes include: tanks, circulation, solids capture, biofiltration, aeration, disinfection, and temperature control. In addition, systems or protocols are needed for feeding, monitoring water quality and biosecurity.
Design of classroom system
Based on space limitations, it was decided to utilize several tanks of different sizes to allow growout of fry in small tanks (two semi-square PolyTanks, 50 gallons) and then final growout in a larger tank (Round PolyTank, 180 gallons).
Starting at the fish culture tank, the discharge water containing both solid and dissolved wastes flows into a centralized sump tank (PT-610 PolyTank, 50 gallons). Water level in the fish tanks is controlled using a center standpipe and to provide an additional backup, an additional standpipe is in the sump. Circulation to both the bioclarifier and the hydroponic systems is then provided by a small, 1/8-HP pump with a screened inlet in the sump. The pumped water then flows to the primary bioclarifier, (bubble-wash bead filter). The bead filter removes the settleable and suspended waste solids, fine and dissolved solids and biologically converts the ammonia to nitrite and then to nitrate.
Deep water raft with floating insulation board growing lettuce, peppers, collards and cucumbers.
Aeration is provided by air stones in each of the tanks, the sumps and also in the deepwater rafts beds for the plant roots. These also provides for a limited removal of carbon dioxide, although not critical due to the low stocking densities used in school aquaponics systems. Finally, a small UV (40-watt HO UV Sterilizer) was placed in-line just after the bead filter to help reduce bacteria loading.
Although not critical, this did help with the application for a health certificate from the state required to serve the hydroponic leafy greens in the cafeteria. A simple automatic feeding system was installed using commercial vibratory feeders. Heating was provided using a 1.0 kW IHC PTC Heater and controller.
Finally, a monitoring and control systems was constructed around a commercial phone system, which monitored water and ambient air temperature, and high/low float switches in the sump and sends a text message if they move outside of acceptable ranges. In addition, dissolved oxygen, pH, temperature, alkalinity and electro-conductivity were routinely monitored to assure optimum water quality for the fish and adequate levels of nutrients for the plants.
Two types of hydroponic systems were constructed, two 1.2 x 4.8 meters, 0.25 meter-deep media beds using expanded clay pellets and three 1.2 m x 4.8 m x 0.25 m water raft systems using floating insulation to support the plants. Each of the beds was constructed of standard framing lumber, lined with insulation to protect the liner which was a simple home DIY pond liner.
Major Equipment | Cost |
Semi-square Polytank 50 gal 27" X 27" X 20" (2) | $317.34 |
PT-5228 round Polytank 180 gal 52" diameter X 28" depth (1) | $320.17 |
Bubble-washed bead filter | $1,072.74 |
Pump 1/8 HP 115/230v | $533.33 |
Polytank sump tank 22" X 22" X 36" PT-610 52 gal | $194.65 |
In Air Stones (3) | $20.64 |
Vibratory feeder 0.5L (3) | $177.74 |
IHC PTC heater and controller (1.0 kW) | $468.00 |
Parts kit (PVC fittings, pipe, misc. fittings) | $500.00 |
Misc. parts and supplies | $150.00 |
Perspectives
Total system cost was approximately $5,000 depending upon the type of media used in the two media beds. One of the significant advantages of this engineering design is that it will require minimum maintenance and will last years. By removing the suspended solids with the bead filter, potential clogging of the media beds and fouling of plant roots is eliminated. Currently, the system is stocked with small Koi carp and tilapia, which are being growout in the larger tank.
An incredible diversity of plants is being raised including numerous types of herbs, leafy greens and vegetables. The system has been operating for over a year and no significant problems have occurred in that time. The bead filter is back flushed on a weekly basis, and nursery seedlings are planted and mature plants are harvested daily.
Có thể bạn quan tâm
Phần mềm

Phối trộn thức ăn chăn nuôi

Pha dung dịch thủy canh

Định mức cho tôm ăn

Phối trộn phân bón NPK

Xác định tỷ lệ tôm sống

Chuyển đổi đơn vị phân bón

Xác định công suất sục khí

Chuyển đổi đơn vị tôm

Tính diện tích nhà kính

Tính thể tích ao hồ