Can an oyster-shell paint help rethink artificial reefs?
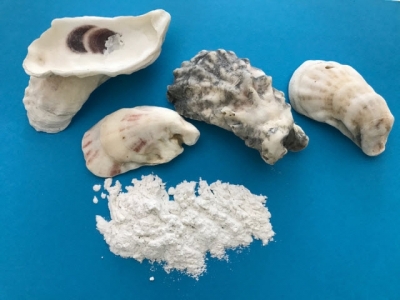
Shellbond’s creative thinking aims to transform natural byproduct into aquaculture’s advantage
A North Carolina company’s patented process breaks the chemical bond of animal skeletal materials like oyster shells and mixes the white powder with other organic ingredients to create a unique paint. Photo courtesy of ShellBond.
A bag of shells might be the perfect spot for oyster spat to settle but shoveling shells into burlap bags and hauling the artificial reefs into the water requires a significant amount of effort for oyster farmers.
“It’s a primitive and labor-intensive process,” said John Hayes Ph.D., oceanographer and managing partner of ShellBond.
A sustainable material made from those same oyster shells could provide a simpler solution.
Through a patented process, animal skeletal materials like oyster shells are heated, cooled, added to water and reheated until the chemical bond is broken and the shells disintegrate. The resulting white powder – called ShellBond – can be mixed with other organic ingredients to form a shell-based paint.
Rather than filling burlap bags with oyster shells, growers can brush the paint onto cages, concrete blocks, grids and other surfaces to create attractive spots for oyster spat to settle. The paint provides the same calcium carbonate-rich environment with less bulk and more options for configuration within the tanks or cages.
“We think we can grow oysters that are bigger, badder and denser with a lot less labor,” said Hayes.
Although ShellBond has potential to improve shellfish farming, the original product had a much more old-school application.
A brick mason named Norman Filbert patented ShellBond in 1989 as a mortar made from marine shells. Burnt oyster shells were the basis for the lime used in traditional building materials, including concrete and mortars used in early settlements such as Colonial Williamsburg, Va. But Filbert believed the product had applications in ocean science, too. When the patent expired in 2006, he approached Hayes about exploring other uses for the calcium carbonate creation.
The pair received further patents to use ShellBond to mitigate environmental pollution, create protective coatings and restore coral reefs. Although Filbert died in 2008, Hayes continued the work, pursuing opportunities to improve marine environments with the product.
ShellBond could also be used to soak up oil spills; remove ammonia and suppress algae blooms in hog lagoons. It could even add pigmentation to farm-raised salmon. Flocculating organic waste material from hog farms and extracting an antioxidant from the liquid creates a natural (non-petroleum-based) that adds the desired red color to the farmed fish, according to Hayes.
But, with Shellbond’s headquarters in Wilmington, N.C., reinvigorating oyster beds along the coastline and helping hatcheries build thriving oyster populations are top-of-mind.
Lawrence B. Cahoon, Ph.D., professor of marine biology at the University of North Carolina Wilmington has consulted on the project, publishing an article in the Journal of the North Carolina Academy of Science about the effect of the oyster shell compound on hog lagoons. He believes ShellBond has “real potential” to transform aquaculture.
“It’s cost prohibitive to collect oyster shells and carry bags in a large-scale aquaculture operation,” he said. “When you can recruit oyster spat to settle on a substrate of almost any shape or configuration, it gives you a lot more options for design and deployment.”
John Hayes pitches at Fish 2.0 in November 2017. Photo courtesy of Fish 2.0.
Thanks to massive state-run waste sites for oyster shells in coastal North Carolina, the raw materials for ShellBond can be acquired at virtually no cost (the material can also be made from clam shells and animal bones, which can be sourced at limited expense).
The rest of the road to commercialization, however, is expensive – and the funding required to go from research and development to field testing has proven challenging.
No large-scale field tests have been conducted since the second round of patents (for marine applications) were issued 12 years ago.
Hayes attempted to secure funding to deploy ShellBond after the BP oil spill in the Gulf of Mexico in 2010 but was unsuccessful. The potential of the biodegradable material for oil spill remediation remains untested. And its aquaculture applications are also unproven.
Hayes estimates it will cost upwards of $300,000 to deploy ShellBond on multiple oyster farms to determine whether the material can have a significant impact on oyster spat sedimentation ratios and oyster quality and density in aquaculture. Until the results of those tests are in, commercialization is stalled.
In addition to participating in pitch competitions such as Fish 2.0 (where ShellBond was a finalist) and One18: The Alltech Ideas Conference, Hayes is pursuing $50,000 in funding through an NC IDEA grant and networking with potential investors.
Hayes might be stymied by the versatility of his own creation. The number of diverse uses for the product coupled with a desire to explore the potential of each (rather than testing and commercializing one at a time) makes it challenging to gain traction.
“There are so many applications and not enough time or money,” Hayes lamented, insisting that aquaculture holds the most promise.
“If we’re going to feed the world, we need be more efficient and sustainable,” Hayes said. “I’m excited to awaken the industry to new and exciting ways to do it.”
About Author: Jodi Helmer is a North Carolina-based journalist who writes about the intersection of agriculture, aquaculture and business.
Related news
Tools

Phối trộn thức ăn chăn nuôi

Pha dung dịch thủy canh

Định mức cho tôm ăn

Phối trộn phân bón NPK

Xác định tỷ lệ tôm sống

Chuyển đổi đơn vị phân bón

Xác định công suất sục khí

Chuyển đổi đơn vị tôm

Tính diện tích nhà kính

Tính thể tích ao