Land-based drip-irrigated culture of sea lettuce
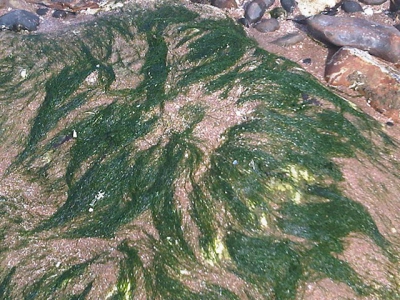
Testing culture design, nutrient concentration on biomass production, protein content
This study demonstrated that green seaweeds like Ulva compressa – seen here in its natural environment and found in North America, the Mediterranean Sea, and throughout Africa and Australia – can produce a sustainable source of protein in land-based systems with less water requirement for biomass production.
The use of recirculating drip irrigation culture methods for growing macroalgae like sea lettuce in controlled environments on land is a new and mostly untried practice.
Because this method conserves water and nutrient resources, it could enable inland culture of seaweeds in high-yield, partially automated aquafarms. The method can also be used for effluent clean-up and water recycling for fish and shrimp culture in an integrated multi-trophic (IMTA) approach. In addition, and when practiced in simple plastic film-covered greenhouses, the method allows for daytime introduction of carbon dioxide-rich flue gases (a mixture of combustion products including water vapor, carbon dioxide, particulates, heavy metals and acidic gases) from industrial point sources directly into head-spaces of the plastic-covered greenhouses, providing inexpensive, recycled inorganic carbon to the drip-irrigated seaweeds.
Another important advantage of this land-based cultivation, including the drip irrigation methods, is the ease and flexibility of controlling the culture system. This ensures that production meets high quality standards and biosafety for human and animal consumption, as well as for other high-value applications such as cosmeceutical or pharmaceutical products. For these reasons, there have been significant attempts of land-based seaweed cultivation, especially in western countries.
The green seaweeds or sea lettuces (Ulva spp.) are ideal candidates for land-based cultivation for many reasons. Research has shown that these species have high growth rates and biomass yields and provide effective bioremediation benefits. As whole dried biomass, they can be a good source of marine protein for inclusion into aquafeeds. This seaweed group is dominant within marine littoral zones from around the world, where it grows prolifically and vegetatively in thick, green mats.
This article – summarized and adapted from the original publication (https://doi.org/10.1371/journal.pone.0199287) – reports on a study to test three drip irrigation cultivation platform designs against fully-submerged controls, over a range of fertilizer concentrations, to test growth response, protein content and overall areal biomass productivity in order to support projecting capital costs and operating expenses for hypothetical scale-up of land-based seaweed farms to supply high-protein seaweed meals to aquafeed mills. This research was supported by Research Grant Award No. US-4599-13R from BARD, The United States-Israel Binational Agricultural Research and Development Fund.
Fig. 1: Seaweed cultivation platforms of Ulva compressa grown at different fertilizer mix (JSM; mean ± SD, n = 3) concentrations on three different cultivation spray systems for 15 days. Multi-Level Horizontal Design (MLHD); b) Bag-Pocket Vertical Design (BPVD), c) Sloped Design (SD), d) Submerged (SUB). Except for the submerged, the other three designs were recirculating systems where the recycled water was pumped back into a reservoir that collects the water and then it drips back into the culture through gravity at a flow rate of ~5 ml per second. https://doi.org/10.1371/journal.pone.0199287.g001
Study setup
The Ulva compressa (UC-CC-ST1) starter biomass used in this study was in unialgal culture at the Marine Biotechnology Laboratory of the University of Connecticut in Stamford, Conn., USA. The strain of U. compressa was originally collected from Bridgeport, Conn. The initial biomass weight of Ulva used for each experimental treatment (eight in all, three experimental designs x 2 replicates, plus 2x SUB controls) was 12 grams wet weight ± approx. 0.25 grams per treatment. Biomass wet weight and ash free dry weight (AFDW), pH, Chlorophyll (Chl), light level, nutrients (N and P), and protein content were analyzed for each treatment at the beginning and at the end of the experiments.
Three drip irrigation platform designs were evaluated and tested in triplicate. The first was a Multi-Level Horizontal Design (MLHD), with three, identical, vertically-stacked and tightly coupled square plastic containers (8” x 8” base x 3” height). The second platform design was termed a Bag-Pouch Vertical Design (BPVD), e.g., a vertical-array of three small clear plastic mesh bag-pouches were tied one above the other on a long poly string. The third platform design was named a Sloped Design (SD), and was built from 50-ml plastic laboratory culture tubes cut into half-sections and arranged in a horizontal sloping formation. For the submerged control treatments (SUB), the treated seaweed pieces were free-floating in the treatment container, which was continuously recirculated using a small, screen submerged aquarium pump.
Fluorescent light banks controlled by a timer to provide a 12:12 hr. light/dark cycle, provided a uniform lighted environment for all culture containers. Room air temperatures ranged from 22 to 24 degrees-C, and salinity of the culture media varied and ranged from 33 to 35 ppt. To fertilize the seaweed masses used in the culture experiments, Jacks Special fertilizer mix was used, (JSM; Jack’s Special™ #77440, J.R. Peters, Inc., Allentown, PA, USA; N:P:K = 21:8:18). Fertilizer treatments were prepared at 1X, 2X, 4X, and 8X stock concentrations in each media.
For additional information on the experimental setup, data collection and analysis, consult the original publication.
Results and discussion
Comparing the mean daily dry biomass productivity from the three drip irrigation platforms to the submerged control platform showed that the submerged control platform consistently maintained the highest biomass productivity, ranging from 20 to 30 grams per square meter per day, whereas biomass productivity for the three drip-irrigated platforms ranged from 5 to 18 grams per square meter per day (Fig 2).
Fig. 2: a) Mean biomass production per day of U. compressa grown at different JSM concentrations (1X-8X) on three different cultivation drip-irrigated system cultivations for 15 days in culture; (mean ± SD, n = 3 replicates; note: each replicate is an average of three trials); b) Percent growth rate per day of U. compressa grown at different JSM concentrations (mean ± SD, n = 3) on three different cultivation spray system cultivation for 15 days.
The high dissolved inorganic nitrogen (DIN) uptake rate observed for the BPVD platform design corresponds to a considerably higher protein content of the harvested biomass for that platform (Fig. 3). For the nutrient treatments, the 1X fertilizer concentration treatment in the SUB control group showed significantly lower protein content than did the 2X, 4X and 8X concentrations for the three drip irrigation platforms. This result indicates that protein content of the biomass produced using the three drip culture platforms was equal or higher than that of the biomass cultured using the SUB control.
Our results showed that both the sloped (SD) drip culture platform design and the multi-level horizontal design (MLHD) produced significantly higher rates of NO3uptake when compared to the totally submerged controls (SUB). Additionally, the bag-pouch vertical drip culture platform design (BPVD) produced the highest uptake rates of NH4+and PO4-3 when compared to the SUB controls.
It is well documented in the literature that water motion is important for uptake of dissolved nutrients (e.g. ionic compounds) into seaweed cells from the surrounding media via active transport and passive diffusion. Thus, the increased water motion experienced by intertidal species can enhance mass transfer rates for gases and nutrients, as is the case for our drip irrigation methodology, where the water motion onto and off of the seaweed thalli (breaking down diffusive boundary layers) can greatly increase mass transfer rates.
Pigment content of the harvested biomass Chl a, Chl b and carotene was highest for the biomass grown using the SD culture platform and enhanced in that treatment when compared to the pigment content in the fully-submerged controls. These results indicate that pigments, per se, are not necessarily a controlling factor directly affecting the biomass production in U. compressa, at least not under the moderate levels of illumination applied in this study.
Fig. 3: Percent protein content of U. compressa grown for 15 days in the different cultivation systems at different concentration of JSM media (mean ± SD, n = 3).
Intertidal seaweeds are potentially susceptible to photo-inhibition of growth, since high light levels in the shallow inter-tidal has been correlated with reduced rates of photosynthesis. This is due to the general observation that the photochemical apparatus of most intertidal seaweeds operates to optimize photosynthesis at low light conditions associated with full immersion. Accordingly, these light-mediated physiological responses will need to be taken into consideration for appropriate species selection for drip irrigation culture in the proposed high-light greenhouse environments where species from the high intertidal littoral zone should be better adapted to the higher light levels than species adapted to growth and survival in the sublittoral or even the eulittoral (mid-littoral) zones.
Our data showed a moderate decrease in the mean biomass productivity with the different drip-irrigated configurations (e.g. range of 5 to 18 grams per square meter per day), although the highest productivity (18 grams per square meter per day), was essentially the same as the lower range of the submerged controls, namely 20 grams per square meter per day. However, we did measure an increase in total protein content for the drip-irrigated cohorts over that of the fully-submerged controls, indicating that the drip-irrigated seaweeds received sufficient water emersion and nutrient uptake to biosynthesize inorganic nutrients to organic cellular products.
Although mean biomass production for the drip-irrigated biomass was somewhat lower than that for the fully submerged controls, the overall benefits of employing the drip irrigation method – 80 percent water savings, higher nutrient removal rates, nutrient conservation and recycling; and the ability to use industrial flue gas for low-cost carbonation of seaweed photosynthesis – should compensate for any minor reductions that might be experienced in overall biomass production at commercial scale.
This simple lab-study has demonstrated that drip-irrigated Ulva seaweed grown using a vertically oriented culture platform can exhibit improved protein content of cultured biomass when provided excess macronutrients. The bag-pouch vertical support design (BPVD) represents a new platform design for culturing Ulva and other seaweed biomass to better utilize the vertical (volume) space and scattered light within a three-dimensional, fully wetted greenhouse environment. The hanging BPVD required less energy to catalyze protein production within the plant thalli than did the other two drip-irrigated designs, and/or the fully submerged control designs, while producing higher protein content biomass than either of the other drip designs tested, and/or the fully submerged tank culture methodology.
The protein content results found in our study for the drip irrigation platforms (~27 percent of dry weight matter) is double the values reported for Ulva rigida grown in offshore fish farm pens and is similar to protein content of Ulva spp. grown in outdoor drip-irrigated culture in Israel using fish farm effluents. On a calculated basis, we estimate that it would require 4,000 μM of DIN to produce 230 μg per gram dry biomass per day of protein in an Ulva drip-culture greenhouse enclosed biomass production system.
The use of the bag pouch design (BPVD) tested in this study as a model for a scaled-up commercial prototype system would allow for better use of vertical space within a semi-enclosed culture environment (a greenhouse), and thus increased productivity on a given land-area basis, versus a one-level horizontal culture design. Due to the slim design and transparent plastic platform, the easy to construct and clean BPVD design also minimizes mutual light shading, which would improve overall biomass and areal productivity from a given land footprint area. The Multi-Level Horizontal design (MLHD) provided the highest growth rate observed when using 2X concentration of Jacks Special Media formulation (JSM), so it too could be considered as a viable candidate for trials in a scaled-up commercial prototype seaweed drip-irrigated seaweed production system.
Perspectives
Results of our study provide baseline information that demonstrates that seaweeds can produce a sustainable source of protein in land-based system with less water requirement for biomass production. Protein production from seaweeds using land-based approaches offers opportunity to support increasing demand for high protein ingredients for animal feeds.
Development of new markets for Ulva land-based cultivation could help promote new environmentally friendly seaweed culture businesses. For example, development of seaweed-based shrimp aquafeeds could increase the sustainability of the intensive shrimp culture industry and for supporting more inland aquaculture of shrimp.
In addition, Ulva is a promising candidate for remediating wastewater effluents, for example from fed fish aquaculture in integrated multi-trophic aquaculture systems before effluents are released into natural receiving waters.
Authors:
Wilson Mendoza, Ph.D. Dominick Mendola, Ph.D. Jang Kim, Ph.D. Charles Yarish, Ph.D. Alyssa Velloze, Ph.D. B. Greg Mitchell, Ph.D.
Related news
Tools

Phối trộn thức ăn chăn nuôi

Pha dung dịch thủy canh

Định mức cho tôm ăn

Phối trộn phân bón NPK

Xác định tỷ lệ tôm sống

Chuyển đổi đơn vị phân bón

Xác định công suất sục khí

Chuyển đổi đơn vị tôm

Tính diện tích nhà kính

Tính thể tích ao