Marine Shrimp Biofloc Systems: Basic Management Practices
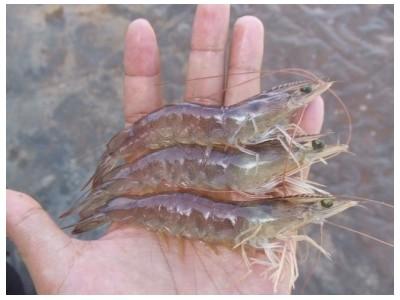
This publication summarizes basic management practices for the majority of farmers raising marine shrimp (Litopenaeus vannamei) in Indiana, US, based on the most current literature available, writes Robert Rode, Purdue University.
Over the past few years an increasing number of marine shrimp enterprises have started up in Indiana. These operations garner attention because of their lower capital costs, their variable scale of production, and shrimp’s high market price.
Based on feedback from a 2014 meeting with Indiana shrimp farmers, it appears that both novice and experienced farmers need more technical knowledge. This publication summarizes basic management practices for the majority of farmers raising marine shrimp (Litopenaeus vannamei) in Indiana based on the most current literature available.
The predominant method of rearing shrimp in Indiana uses the biofloc water treatment system for dealing with the metabolic wastes associated with production. The majority of the discussion to follow deals with this kind of system.
Water Quality
No matter what system is used, shrimp must have good water quality for health and growth.
Shrimp, like other aquatic organisms raised at higher than natural densities, affect the quality of the water they live in. Controlling this environment to maintain optimum conditions reduces stress levels, improves growth, and reduces the risk of mortality. Recommended ranges for water quality parameters for shrimp culture are listed in Table 1. Owner/operators must manage these parameters on an hourly, daily, or weekly basis with either infrastructure and equipment or additions to the rearing system.
A number of water quality testing kits/ probes are available at various prices. Whatever the testing mechanism, the kit must be for saltwater applications. Methods of controlling water quality will be described later in this text.
Biofloc Systems
Biofloc systems remove metabolic wastes from aquatic production systems. They replace biofilters in a classic clear water Recirculating Aquaculture System (RAS). Bacteria that convert ammonia to nitrate are cultured in the main rearing tank as opposed to in a separate vessel. The bacteria form aggregates or colonies (called bioflocs) suspended in the water column. This is done for several reasons. Eliminating the biofilter reduces costs and saves floor space. In the case of shrimp, the biofloc becomes an additional feed source, which decreases the feed conversion ratio of commercial feeds, again reducing costs.
Shrimp Stocking and Feeding
Shrimp are stocked in biofloc systems at densities ranging from 250 to 500 post-larvae (PLs) per square meter. Production for these systems ranges from 3–7 kg/m² and/ or 3–9 kg/m³. Feed conversions should range from 1.2:1 to 1.6:1. Microbial proteins in the biofloc generally add 0.25–0.5 additional growth units for every one unit of commercial feed. Production parameters for these systems are shown in Table 2.
Shrimp are stocked in single batches of like-size postlarvae (PLs). Feeding is based on calculations of biomass, feed conversion, mortality, weekly gain per individual, and percentage body weight feeding.
Feed rate is adjusted after routine sampling for uneaten feed on the bottom of the tank using a dip net one-half hour after feeding. Less than optimum water quality parameters can also be an indicator that feed is less than optimum. Feed can be dispersed either by hand or with a mechanical device such as a belt feeder. Feeding by hand is best for dispersing the feed over a wide area of the tank allowing all individuals to obtain food. Automated feeders can be used when the operator is not present. Processed feed is still the most important addition for good growth of shrimp even in a biofloc system. Shrimp feed should be purchased from a reputable manufacturer and stored properly.
Diets change over the production cycle with pellet size increasing from approximately 1.5 mm up to 2.5 mm as the shrimp mature. Protein and fat content may remain around 40/9 throughout the growing season. If PLs are smaller than recommended, a smaller particle size and higher protein feed is warranted. Please check with feed and PL suppliers as to recommended starter feeds.
An example for calculating daily feed allowance might be as follows:
A 16 ft. pool approximately 3 ft. deep is stocked with 300 PLs per square meter at an average size of 1 g each. How much would the daily feed allowance be after four weeks? Using values from Table 2, the theoretical biomass of shrimp is found.
Starting size of shrimp (1.0 g) x 4 weeks’ growth (1.5 g/week) = 7 g individual shrimp.
Sampling should confirm this.
Diameter of the tank is 16 ft. and converting to meters, 16 ft. is about 5 m,
A = π (2.5 m)² = 20 m²
Stocking 300 shrimp per m² in 20 m² gives us 6,000 individuals at 7 g each or 42,000 g or 42 kg.
If we assume 10% mortality, that is reduced to 37,800 g or 37.8 kg.
Feeding at 4% of body weight would be 37,800 g x 0.04 = 1,512 g or 1.51 kg per day in week four.
Feed can be parceled out continuously or in multiple feedings per day. The choice has to do with mechanization and management style. Shrimp have small intestinal tracts, so multiple small feedings or continuous feeding of the daily feed allowance is recommended. Feeding done multiple times per day maximizes utilization and uniformity of biological processes of waste treatment.
Biofloc Management
The biofloc in the shrimp-rearing tank should be considered a dynamic living organism and must be managed as such. A description of the biofloc and how to “feed” and support the biofloc follows.
The major component of biofloc is heterotrophic bacteria. The function of the biofloc is to reduce the nitrogenous metabolic waste (ammonia, nitrite) produced by shrimp feeding and production.
Ammonia consumed by heterotrophic bacteria becomes protein, which can then be consumed by shrimp and converted into growth. Heterotrophic bacteria need carbon for ammonia to be assimilated. In addition to the commercial feed, a supplemental source of carbon must be added in order to stimulate production of the heterotrophic bacteria and reduce the nitrogenous waste.
Shrimp feed has a carbon to nitrogen (C:N) ratio of approximately 7–10:1. Heterotrophic bacteria would prefer a ratio of approximately 12–15:1. Simple sugars or starches are added to increase the ratio and promote bacterial growth. Additives have included molasses, sugar, sucrose, and dextrose. Some producers use glycerin. The simpler the sugar, the quicker is the response from the bacteria. Application rates will vary with the protein content of the feed and composition of the carbon source, but a good rule of thumb is that for every 1 kg of feed, about 0.5–1 kg of carbon source is required. Higher protein feed will need higher carbon supplementation. Actual applications must take into consideration the levels of ammonia and nitrites in the water.
The choice of carbon source is dependent on price, availability, ease of application, and efficacy. The carbon source should be diluted prior to application no matter the physical state. Solids should be liquefied so as not to sink directly to the bottom and become unavailable. Some liquids, such as molasses, could sink directly to the bottom as well. Dilution allows for gradual application from a holding/dilution tank through a small aperture valve over time to spread the carbon throughout the tank. This same method can be used for alkalinity applications to be discussed later in the text.
Suspended solids are measured to determine the gross quantity of the biofloc for shrimp production. Suspended solids are measured using Imhoff settling cones. Cones have a one-liter volume. The cone is filled, allowed to settle for 10–20 minutes and reading taken by reading the graduations on the cone. Shrimp biofloc should maintain settleable solids at 10–15 mg/l. Readings should be taken at least once weekly.
Increasing the heterotrophic bacteria population also increases the total oxygen demand of the tank. Heterotrophic bacteria require oxygen for life processes such as ammonia assimilation. Additionally, solids in the water column reduce the ability of that water to hold as much oxygen. Oxygen must be added either through aeration with atmospheric air and perhaps supplemental compressed or liquid oxygen. Popular aeration devices include airlifts, air diffuser stones, venturi aspirators, and water pumps. Supplemental oxygen can be incorporated into venturi aspirators or diffuser stones.
Oxygen additions may be combined with the need to keep biofloc in suspension. Without mixing, heterotrophic bacteria colonies will sink and lose the ability to remove ammonia. Mixing is accomplished with the same devices that add oxygen, namely airlifts, diffuser stones, venturi aspirators, and water pumps. The choice of aeration/ oxygenation methods depends on production level and centralization of equipment. High production levels may require use of pure oxygen supplementation. Use of low-pressure, high-volume air blowers can be sized to cover the needs of multiple tanks driving both airlifts and diffusers. Likewise, water pumps can drive multiple venturi aspirators, but are usually sized for individual large tanks.
With high biofloc respiration rates comes production of high carbon dioxide levels (CO2). Any of the methods of aeration/oxygenation will drive CO2 from the water column. Therefore, CO2 usually is not an issue for shrimp. However, CO2 may build up in the atmosphere, depending on the amount of air exchange through the building. Operators need be aware of this both to protect the personnel in the building from CO2 poisoning and because if building air is used for aeration, CO2 also may ultimately build up in the water column.
High feed rates leading to large biofloc populations can be detrimental to shrimp. Total suspended solids (TSS) over 500 mg/l can irritate the gills and stress shrimp. Controlling high TSS can be accomplished by using foam fractionation and/or some type of settling basin such as a swirl separator, radial flow settler, simple clarifiers, etc. These devices can limit the occurrence of high TSS, but do not remove it entirely. Therefore, any method must be controlled either by timing of operation or flow rate through the devices. Good control of solids can be achieved by turning over the rearing tank water every 3–4 days. Clarifiers are sized to contain 1%–5% of system volume and are operated with a flow rate that gives 20–30 minutes of residency time (Hargreaves).
Removal of TSS can also remove alkalinity and nitrate from the system. Alkalinity can be recovered by allowing sediments to undergo either partial or full anaerobic decomposition. Nitrate can be reduced by removing solids from the system. Anaerobic decomposition has several benefits as well as drawbacks. Not only can alkalinity be recovered, but nitrate can be removed by conversion to nitrogen gas, which is released to the atmosphere.
Anaerobic decomposition needs space. In simple anaerobic decomposition, sludge forms in some portion of the system, is allowed to go anaerobic for a short period of time, and then is removed from the system. An example of this would be emptying a settling basin sporadically. Solids can be removed from the system to a separate container/ vessel, allowing anaerobic conditions to occur and then decanting off the “clean” water after sedimentation of solids. When we use these simple methods, the timing and success of anaerobic decomposition is highly variable. One of the potential dangers of anaerobic digestion is the possible production of hydrogen sulfide (H2S). Like CO2, in tightly enclosed spaces H2S can be a danger to both shrimp and humans.
Only a portion of the alkalinity tied to heterotrophic bacteria can be recaptured by anaerobic decomposition. Alkalinity must be supplemented by additions of sodium bicarbonate. Alkalinity should be maintained above 150 mg/l and measured at least twice per week. Alkalinity helps maintain pH above 7.0, so if daily pH readings fall below desired levels a quick check of alkalinity and additions of sodium bicarbonate are warranted. As a guide, it is expected that 0.25 kg of sodium bicarbonate would be added for every kilogram of feed entering the system. Researcher Tzachi Samocha has created a good guide for additions of sodium bicarbonate, soda ash, and sodium hydroxide to control alkalinity and pH. As with carbohydrate additions, sodium bicarbonate should be mixed with water and added to the rearing system gradually for efficient uptake.
Reusing Biofloc System
White Shrimp are grown in single batch units. Prior to final complete harvest, the producer must decide what to do with the water from the harvested system. It can be pumped and stored for reuse or discharged to an appropriate site—or some combination of storage and discharge. Likewise, any sludge collected from settling basins or anaerobic respirators must also be disposed of through some means. Land application is not recommended, as few plants can tolerate salt levels in the soil. For possible means of disposal, please contact the Indiana Department of Environmental Management (IDEM) or the appropriate agency, if outside of Indiana.
There are conflicting research results as to amount of possible heavy metal buildup in biofloc waters and, more importantly, in the flesh of shrimp raised in these waters, which have been used repeatedly for the production of shrimp. In their research, Tzachi Samocha and others found no accumulation of heavy metals in water or culture media stored for reuse. In other recent research, Leffler and Brunson found that arsenic, cooper, iron, manganese, molybdenum, selenium, and zinc all increased significantly in the water over the course of an 18-week grow-out period. Likewise, arsenic, lead, molybdenum, and selenium increase significantly in the shrimp flesh over the same period. Samocha suggested that preliminary observations show that accumulations may be a factor of feed used. In any case, producers need be aware that the amounts of significant compounds will increase and/or decrease over time in a biofloc system. This may impact the performance of shrimp and their quality.
Related news
Tools

Phối trộn thức ăn chăn nuôi

Pha dung dịch thủy canh

Định mức cho tôm ăn

Phối trộn phân bón NPK

Xác định tỷ lệ tôm sống

Chuyển đổi đơn vị phân bón

Xác định công suất sục khí

Chuyển đổi đơn vị tôm

Tính diện tích nhà kính

Tính thể tích ao